|
|
|
发表人:jdata |
发表时间:2011/1/12 10:59:00 |
|
|
本栏论题: |
一窑四线平拉玻璃熔窑设计 [6432] |
唐福恒 盛利军(秦皇岛玻璃工业设计研究院秦皇岛市066001)
摘要 介绍了260~300td一窑四线平拉玻璃熔窑的设计情况,包括:熔化部设计,分支通路的布置原则,分支通路长度尺寸的设计,全窑池底结构形式和不同池深的窑底结构处理。
关键词 平拉玻璃 熔窑设计
天津玻璃厂是我国采用平拉工艺(格法)生产平板玻璃的重点骨干企业。该厂于1986年全套引进了比利时格拉威伯尔公司(Glaverbe1)的平拉玻璃生产技术及主要设备。建设初期为一窑二线,并留有可热接第三线的接口。后来在不停产的情况下,成功地热接了第三线,建成了国内第一条一窑三线的平拉玻璃生产线。长期稳定地生产2 mm厚优质薄玻璃,工厂取得了良好的经济效益,同时为国内多家平拉玻璃企业提供了技术支持。
随着天津市城市建设的发展和环境保护的要求,该生产线所在的地理位置已被规划为商住区,玻璃厂需要搬迁到新址。由于原一窑三线已经完成了两个窑期近17年的运行,拆后可利用的设施已不多,以及要扩大生产能力的考虑,工厂决定新建一条一窑四线平拉玻璃生产线。设计熔化能力260~300t/d,燃料为重油,窑龄8年,玻璃原板宽
度4000 mm,耐火材料立足于全部国产,现将有关设计情况介绍如下:
1 熔化部设计
在80年代引进的一窑三线平拉玻璃熔窑,从窑型尺寸到各部位细部结构看,该熔窑的熔化部在现在看来仍是一座200 t/d级的技术比较先进的熔窑。本次工厂搬迁需要新建同样技术先进的一窑四线,熔化能力为260~300 t/d的熔窑,并要积极采用近年来的各项熔窑新技术。
本设计确定一窑四线平拉玻璃熔窑的熔化部,采用近年来在国内浮法玻璃熔窑上广泛采用的熔化部结构形式,并以某建成投产多年的300 t/d浮法线熔窑做为参照,进行熔化部设计。
1.1 熔化部主要尺寸的确定
按照熔化部的池宽尺寸计算公式:
B=9000+ (P-300) ×7
求得该熔窑(按P=300 t/d)的熔化部池宽为:B=9 000 mm。
对于浮法玻璃熔窑来说,熔化部和熔化区的长宽比分别为:K1=3~3.3;K2=1.8~2.0。对于平拉玻璃熔窑来说,为了保证长通路末端玻璃液的成形温度,这两个比值要取得小一些,初步设定熔化部的长宽比为:K1=2.9;熔化区的长宽比为:K2=1.85。计算出熔化部和熔化区池长的初步尺寸:
熔化部池长:L=9 000×2.9=26100 mm,
熔化区池长:Ll=9 000×1.85=16650 mm。
根据这两个初步的长度尺寸设定以下数据:
1#小炉前长:La=3500 mm,
小炉对数:Pn=5
小炉中心线间距:1#~4#:3100mm,4#~5#:2900mm ,
5#小炉后长:Lz=10300mm。
与浮法熔窑相比,末对小炉后的尺寸要偏小一些,主要是为了提高进入通路的玻璃液温度,以保证通路末端玻璃的成形温度。根据以上的设定数据,求出一窑四线熔窑的熔化区和熔化部的实际池长尺寸如下:
熔化区池长:3500+3100×3+2900+1000=16700 mm。
熔化部池长:3500+3100×3+2900+10300=26000 mm。
熔化部池深:1180 mm (同一窑三线)。
1.2 投料池结构
20世纪90年代出现的“全窑宽投料池”结构,对于大型横火焰玻璃池窑来说是一项重要的新技术。近年来,国外新建或改建的大型横火焰玻璃熔窑上多已采用了全窑宽投料池结构。全窑宽投料池的优点是:投料口结构简单、增加熔窑的熔化能力、提高玻璃液的熔化质量、节能降耗、节省建设投资。国内多家玻璃厂已在新建或改扩建的熔窑上采用了全窑宽投料池结构,取得了良好的经济效果,显示了全窑宽投料池的优势,已是国内一项成熟可靠的玻璃熔窑新技术。本一窑四线熔窑确定采用全窑宽投料池:池宽9000 mm,池长1700 mm。前脸墙采用L型吊墙及其配套密封设施。
l_3 燃烧系统
原一窑三线熔窑为4对小炉,采用顶插式燃油喷枪,顶插式喷枪燃烧效率高,在大型玻璃熔窑上常被采用,但这种喷枪目前国内还无厂家生产,需要引进。而另一种在国内玻璃熔窑上大量采用的“炉下式燃油喷枪”,也是燃烧效率较高的喷枪,国内有多个厂家生产此种喷枪及系统,配套方便。炉下式燃油喷枪在操作和维修方面,比其他类型的喷枪都简单容易。本一窑四线熔窑确定采用国产的炉下式燃油喷枪及配套系统,5对小炉,每个小炉两支枪。
2 通路设计
通路是平拉玻璃在进入成形室之前要经过的关键部位,此部位直接关系到平拉玻璃产品的产量和质量。一窑四线的通路设计是按以下的原则进行的:首先根据生产操作要求确定好四条分支通路的分布位置形式;然后根据通路温降情况和通路结构要求确定各分支通路的长度;最后在通路窑体结构上进行配套设计。
2.1 四条分支通路横向分布尺寸的确定
原一窑三线的通路布置形式为:直形横通路连接三条平行的分支通路,运行17年多来效果良好,是很成熟的“宽板深池”通路结构。本次一窑四线设计确定:横通路仍采用直线形的,后面连接四条平行的分支通路,横通路和四条分支通路对称布置在熔窑纵向中心线延长线的两侧。玻璃原板宽度4 000 mm 的分支通路,其通路砖结构的外宽约为5800mm,钢结构外宽约为7000mm。各平行分支通路中心线间距尺寸的要求是:对于需要有更换转向辊操作位置的,最小尺寸为12000mm;对于无更换转向辊操作位置的:最
小尺寸为8500 mm。根据这样的尺寸要求,4条分支通路中心线的横向间距分布尺寸,考虑了以下两个方案:
方案1:12000+8500+12000=32500 mm,
此方案是考虑更换转向辊的操作位置为两处,分别在1#与2#分支通路之间和3#与4#分支通路之间。
方案2:8500+12000+8500=29000 mm,
此方案是考虑更换转向辊的操作位置为3处,分别在1# 、4#分支通路的外侧和2与3分支通路之间。
方案1的1#和4#分支通路外侧不需更换转向辊操作,只需留有人行和物流通道即可,对于玻璃原板宽度为4000 mm 的通路来说,分支通路的半宽加上通道之和的尺寸应不小于6000 mm,这样一窑四线的通路区域工作面的总宽度尺寸最小为:6000+32500+6000=44500mm,需要配跨度为45000mm的厂房。
方案2的1#和4#分支通路外侧要进行换转向辊操作,需要留有较宽的尺寸,对于玻璃原板宽度为4000 mm 的通路来说,通路半宽加换辊操作空间尺寸应不小于9000 mm,则通路区域的工作面总宽度尺寸最小为:9000+ 29000+ 9000=47 000 mm,这就需要配跨度为48000mm的厂房。
比较这两个方案,可见方案1具有优势:厂房跨度少3000mm、换转向辊操作位置少1处、换辊用的天车运动区间也小,由此本项目选定了方案1做为四条分支通路的横向间距尺寸。
2.2 各分支通路长度尺寸的确定
确定了4条分支通路的横向分布尺寸之后,再根据通路温降情况和通路结构要求确定各分支通路的长度尺寸。为了表达方便,首先定义一个术语——“通路起点”,它是指熔窑纵向中心线与横通路中心线交点处。
根据热工计算和现场测定,能够确定出原一窑三线的通路起点和3条分支通路的C形砖前的温度。实测结果与计算结果略有不同,边部的两条支通路(1#和3#)C形砖前的温度比中部的2#通路平均高出20℃左右。为什么会出现这种情况呢?
分析原因可能主要是中间通路离卡脖较近,产生回流的玻璃液比边部通路的多一些,多带走了一些热量所至。实际生产中也是边部通路末端温度偏高,拉引量偏低,与测定结果一致。搞清楚这一点对于掌握一窑多线的各通路温度情况是很必要的。
根据原一窑三线通路区域的温度制度,结合新设计一窑四线通路区域的窑体结构变化情况,特别是窑体的保温结构情况,可以确定出一窑四线熔窑的玻璃液在通路区域不同区段里的温度变化情况。
在本次设计中,考虑到4条线的布置需要,各分支通路长度要比3条线的加长一些。但仍要保持各分支通路c形砖前的温度,经过多次计算进行优化,本设计确定将“通路起点”玻璃液温度要略提高一些,从同吨位浮法玻璃熔窑的温度制度来看,这是不难办到的。确定好了一窑四线通路区域的温度制度,就可以确定各部位通路的长度尺寸了。计算结果,一窑四线的通路起点到C形砖前的长度为:17000 mm,到板根处为:18750 mm。
根据前面已确定好的各分支通路横向布置尺寸,中间的2#和3#分支通路从横通路中心线算起到板根处的长度为:18750-(8500/2)=14500mm;边部的1#和4#分支通路这一长度为:18750-(8500/2)-12000=2500mm。
显然2500mm是太短了,不能满足分支通路末端的结构设计要求,必须加长。根据分支通路末端的结构情况,边部1#和4#分支通路的这一长度最小应为6250 mm。由此边部的1#和4#分支通路从通路起点到板根处的长度是: (8500/2)+12000+6250=22500mm,到C形砖前的长度为:22500-1750=20750mm。按这一长度计算,边部的1#和4#分支通路到C形砖前的温度要比中间的2#和3#分支通路温度低近30℃ ,这是按玻璃液在各分支通路区域的温降速率相同时的计算结果。前面已述及一窑三线的边部通路温度要比中部的平均高20℃左右,一窑四线的边部分支通路也会出现这一情况,因此边部的1#和4#分支通路C形砖前的实际温度可以达到设计的温度。
至此,一窑四线平拉玻璃熔窑的通路布置平面尺寸就全部确定好了。一窑四线平拉玻璃熔窑平面简图见图1。
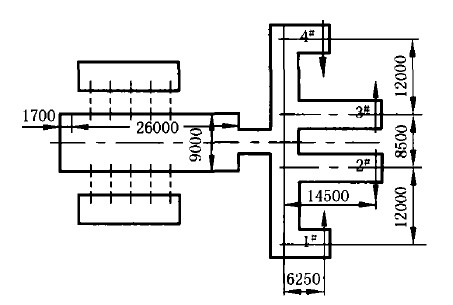
图1 一窑四线平拉玻璃熔窑平面简图
3 窑底结构设计
原一窑三线熔窑的窑池深度为:熔化部池深1180mm,通路池深1265mm,相差85mm。池底
砖结构总厚度也不同,分别是:熔化部570mm,通路485mm,也相差85mm。熔化部与通路两部分的池深与池底砖结构厚度之和正好相等,全窑池底砖结构下平面标高相同。
新设计的一窑四线熔窑的池深与原一窑三线的相同:熔化部1180mm,通路1265mm。在窑底结构上,特别是池底铺面结构做了比较大的改动:池底铺面砖厚度减薄了,池底大砖厚度适当加厚了些,这种改动在满足设计指标对窑体要求的前提下,可节省近200万元的建窑投资。
熔化部(包括卡脖)池底采用“合页窗式” 活动保温结构,可开可闭,池底砖结构总厚度为550mm;通路池底采用固定保温结构,池底砖结构总厚度为520mm。熔化部与通路两部分的池深与池底砖结构厚度之和不相等,全窑池底砖结构下平面 |
|
|